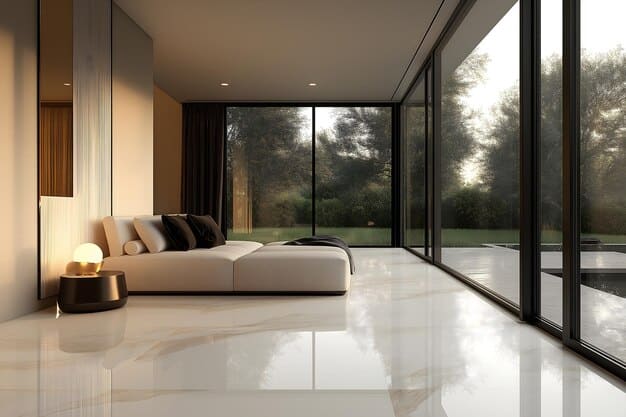
The best glazed porcelain tiles. why Primeasia surfaces?
How We Made Glazed Porcelain Tiles
Primeasia Surfaces is proud of the process of fabrication involved actively in the production of glazed porcelain tiles. From an aesthetic view, these tiles are attractive, and are also designed to withstand the rigors of both wall and floor applications. Advanced technology paired with craftsmanship artistry makes the production of first-rate glazed porcelain tiles a multifaceted endeavor.
Our process of making 100x100cm glazed porcelain tiles involves a number of steps designed to meet the highest standards including wall and floor applications. The production of glazed porcelain tiles is carried out by sophisticated means with the first step being mixing fine clay, feldspar, kaolin, and water to make a slurry. The slurry is shaped into tiles by high-pressure pressing which sets the density and durability standards for the tiles.
After pressing, the raw tiles undergo firing in kilns. The fire temperature is typically around 1200 degrees Celsius. The firing process is integral in making the final tile stronger while simultaneously enhancing the beauty of the tiles. Glaze undergoes initial firing so that the tiles can add color, texture, and finish. The tiles undergo refiring to achieve a surface that is tough, and resistant to water and stain absorption
1. Material Selection:
In terms of the composite materials, the clay, feldspar, and quartz which Primeasia Surfaces use, are all top quality raw materials.
These materials are equally important as they assist in achieving the desired glossy and matte finishes. The process starts with Premium Raw Materials. We use a mixture of fine clays, feldspar, and silica. Selecting these materials is fundamental since it determines the strength and aesthetics of the final product.
2. Formulation and Mixing:
These components are selected, they are transformed into a precise batch. This guarantees uniformity in tile characteristics and appearance. This also enables us to achieve the desired macro and micro design features: glossy and matte finishes.
3. Shaping the Tiles:
Later on, the combined mixture undergoes molding into 100x100cm glazed tiles and it is accomplished with high-end glazing machinery. This process ensures even pressure and density throughout the tile and facilitates uniformity in strength and durability. We offer a broad range of styles and sizes including wall and floor tiles. This range meets most of the architectural needs. The initial pressing step is vital for defining the tile thickness and density. The advanced tiling machines guarantees the mixture is shaped into 100x100cm glazed tiles.
4. Firing Process:
Once shaped, the tiles undergo firing at high temperatures in a kiln.
The former process makes these tiles strong and durable, as they undergo vitrification. Moreover, it also improves the water absorption resistance of tiles much more and hence supports their durability.
5. Glazing:
It is the process of glazing that sets our tiles apart compared to other tile manufacturers. Prior to the final firing, tiles are coated with a thin layer of glazing solution, which increases the bond strength of the tiles. The finished glaze responds to different environmental factors while providing a protective layer which makes it highly functional for both indoor and outdoor tiles. A lot of our clients prefer the finish to be either glossy or matte.
6. Quality Control:
The last step in the process involves thorough quality control screening for every single batch. They are visually inspected for color sameness, strength, and surface finish since our clients expect the best quality glazed porcelain tiles.
How We Made Glazed Porcelain Tiles
Glazed porcelain tiles are produced using elaborate production methods. First, fine clays, feldspar, and kaolin are combined with water to generate a slurry. Then the mixture is shaped into tiles by employing high pressure pressing methods, ensuring those are dense and robust enough. The tiles are then shaped and fired in a kiln with extremely high temperatures somewhere around 1200 degree celsius. The glazing process not only strengthens the structure of the tiles but also drastically improves the aesthetics.
To enhance color, structure, and finish, a layer of glaze is applied to the surface after the first firing. The tiles are subsequently refired for temperature hardening to achieve an impermeable surface that resists water and stain.
Technological Innovations
Digital Printing: Advanced digital printing allows the fabrication of textures and patterns that mimic wood, stone, or marble on glazed porcelain tiles.
Anti-Slip Coatings: Glazed tiles with micro-texturing enhance slip-resistance even when wet.
Eco-Friendly Practices: The environmental impact of tile manufacturing can be minimized through the use of recycled materials and energy-efficient methods.